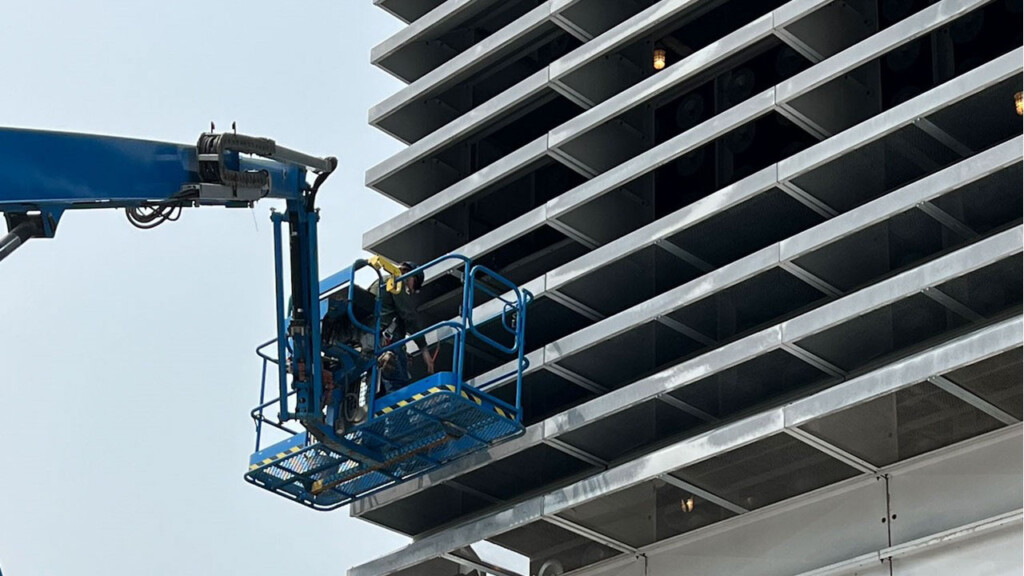
When we think of some of the challenging situations our crews face, there are images of downed electric lines, extreme weather conditions, and the high stress environment of managing power outages. While these are situations they are very familiar with, the team out at Sumpter Power Plant in Belleville, Michigan ran into a problem they hadn’t anticipated.
A Persistent Problem
The guys out at Sumpter may have appeared a little too welcoming, because for the last three years or so, families of birds have made their homes in the air intake structures on-site at the power plant. While baby birds hatching on the Nature Channel is adorable, in real life dozens of birds leave behind abandoned nests, feathers and molt, as well as a whole lotta…you guessed it. While the debris hadn’t affected air flow, due to the diligent efforts by the team to clear it frequently, it wasn’t a permanent solution.
“We just said to ourselves, there’s got to be a better way,” said Generation Manager, Mike Wood.
Tackling the Problem
Keeping the birds out was important to the team, but so was making sure they found a humane way to evict their feathered friends. While experts were advising Wood and the team that poisoned corn was the only real lasting solution, the guys didn’t want to go that route.
“It felt like we had tried everything. We put out owl decoys because they are a natural predator. The birds perched right next to it. We played hawk screeching over speakers,” said Wood. “Those birds just laughed at us.”
Real Solutions
But the Sumpter crew didn’t know how to give up, so they did some additional digging. They eventually found a manufacturer of plastic cooling web, configured almost like honeycomb, that would not only keep the birds out, but would prevent ice or other buildup from impeding air flow through the filters. But then there came another problem. The cost. The webbing was definitely needed, but the additional cost of the installation seemed a little too much. So, the crew took the project over.
A Big Undertaking
Wolverine’s team fabricated the square screens to fit perfectly and then took on the monumental task of installing them. It took immense coordination to get the screens hoisted, maneuvered up seven flights of stairs, with guys working both inside the structure as well as outside of it. While it took about six weeks to complete the installation, tens of thousands of dollars were saved by doing it themselves.
“That’s what most of our job is about,” said Ken Sowards, Chief Plant Operator. “Problem-solving.”
With the screens in place, the filters are working at peak performance and the team isn’t hauling the power washer out to clean up after the former tenants. It seems that all is well that ends well…except…
“Of course, now the birds have started roosting on the fence,” said Wood.
You can almost hear the problem-solving wheels turning.